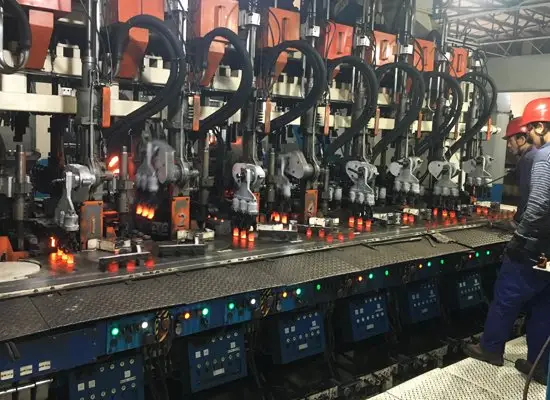
Table of Contents
Roen Glass is a leading manufacturer and supplier of premium glassware products, offering a variety of high-quality drinking glasses and custom glass solutions. With over 25 advanced production lines and cutting-edge energy-efficient kilns, we achieve an impressive annual output of approximately 1 million tons of glassware, with a daily capacity of nearly 950,000 pieces.
In today’s article, we’ll guide you through the comprehensive glassware manufacturing process, shedding light on the raw materials, key stages, and quality control measures involved in creating Roen Glass products.
Raw Materials Used in Glassware Manufacturing
The production of glassware begins with selecting high-quality raw materials. For Roen Glass, we use a variety of ingredients that are essential for producing durable, functional, and aesthetic glass products. Here’s a breakdown of the primary materials involved:
Silica Sand
Silica sand, comprising over 70% of the raw materials in glass production, is the foundation for creating glass. Known for its high temperature resistance and chemical stability, silica sand forms the base of the glass mix. Its cost-effectiveness makes it an ideal material for large-scale glass manufacturing.
Sodium Carbonate
Sodium carbonate, or soda ash, is essential for the melting process. It helps lower the melting point of silica sand and promotes the formation of a liquid glass mixture. This material also reduces the number of air bubbles in the glass, improving transparency and overall quality.
Limestone
Limestone acts as a key agent in the glass production process, helping to remove gases such as oxygen and carbon dioxide, thus preventing bubbles in the glass. Additionally, it contributes to enhancing the hardness and wear resistance of the final product.
Other Auxiliary Materials
Various auxiliary materials are used to modify the physical properties of the glass. These include oxidizing agents, colorants, and texturing agents, which influence the glass’s color, strength, and heat resistance. These additives ensure that the glassware meets the specific needs of our clients, from clear glass cups to colored or textured drinking glasses.
Molds for Glassware Manufacturing
Molds are vital to creating the desired shapes and designs of glassware. The precision and quality of the mold directly influence the final product’s quality. At Roen Glass, we manufacture molds from cast iron for its excellent casting performance and durability. Our molds undergo CNC machining to ensure accuracy, followed by heat treatment processes such as quenching and tempering to enhance hardness and wear resistance.
For mass production, our machines are fitted with 24 pairs of molds, capable of producing millions of glassware units over their lifespan. During the initial production phase, trial runs are conducted to ensure that the molds are functioning optimally, and quality control teams monitor production closely to maintain high standards.
The Glassware Manufacturing Process
The glassware manufacturing process is a blend of high-tech machinery, skilled craftsmanship, and precise control. Let’s walk through each key stage:
Melting of Glass Raw Materials
In this step, raw materials, including silica sand, sodium carbonate, limestone, and a percentage of recycled glass, are placed in a high-temperature furnace. The furnace’s temperature and melting time are tightly controlled to ensure that the materials fully melt and combine into a homogeneous mixture. Each glass product’s unique qualities, such as color and transparency, are influenced by this stage.
Glass Molding
Once the glass mixture has melted, it is dropped into molds, where it begins to take shape. Molding machines use precise mechanisms like pressing and blowing to shape the molten glass into the desired form. For Roen Glass, this step is followed by a rotating platform, ensuring that each mold receives the proper treatment for consistent and flawless products.
Annealing Process
After molding, the glassware undergoes an annealing process in a long kiln, where the glass is slowly cooled. This gradual cooling prevents the glass from cracking due to thermal shock and helps reduce internal stress, ensuring that the glassware is strong, stable, and durable.
Quality Inspection of Finished Glassware
Once the glass products have passed through the annealing furnace, they are carefully inspected for defects. At Roen Glass, we maintain strict quality control processes at every stage of production. Our experienced quality assurance team performs visual inspections and physical tests to check for defects such as bubbles, cracks, and surface irregularities.
Common Glassware Quality Issues and Solutions
Despite the best efforts, glassware production may occasionally present challenges. Below are some common quality issues and their solutions:
- Bubbles: Bubbles may appear on the glass surface due to improper raw material mixing or furnace temperature fluctuations. Solution: Improve material consistency and stabilize kiln conditions.
- Deformation: Deformation is often observed in rounded glass designs. Solution: Inspect and replace molds regularly to ensure precision.
- Surface Roughness: This can occur from oil residues or imperfections on the mold. Solution: Enhance polishing with additional gas spray guns.
- Broken Glass: Any defective glass is removed and discarded. Solution: Strict inspection protocols prevent defective products from reaching packaging.
Packaging Options for Finished Glass Products
At Roen Glass, we provide various packaging options to suit different customer needs, ensuring the safe delivery of glassware worldwide.
Pallet Packaging
Ideal for glassware requiring secondary processing, pallet packaging involves stacking the glassware neatly on a pallet, with protective layers like paper trays between each glass. The pallet is then wrapped securely in plastic film before being moved to the warehouse.
Carton Packaging
For bulk packaging, we use custom-designed cartons that provide ample protection for glassware. Cartons are stacked on pallets and wrapped to ensure they remain intact during shipping.
Custom Labeling and Packaging:
For clients requiring custom labels or unique packaging designs, Roen Glass offers fully customizable packaging solutions, including automated labeling machines and branded packaging.
Conclusion
Understanding the intricate glassware manufacturing process is key to appreciating the craftsmanship and quality behind every product. From selecting premium raw materials to employing advanced molding and annealing techniques, Roen Glass ensures that each piece of glassware is both functional and beautiful.
With a focus on precision, durability, and customization, Roen Glass is your trusted partner in creating high-quality glass products that meet both aesthetic and practical needs. Whether you’re looking for bespoke glassware for your brand or durable, high-performance drinking glasses, our advanced manufacturing process guarantees excellence at every step.